SOPまでの開発プロセス全体を通して、バッテリーの組み立てとテスト
From environmental tests to verify durability and stability of the system, e.g., under different temperatures and humidity rates to endurance and functionality tests, we examine every solution to determine its functional safety, performance, continuous power output, compatibility with other components and ability to cope with different mechanical and electronic loads.
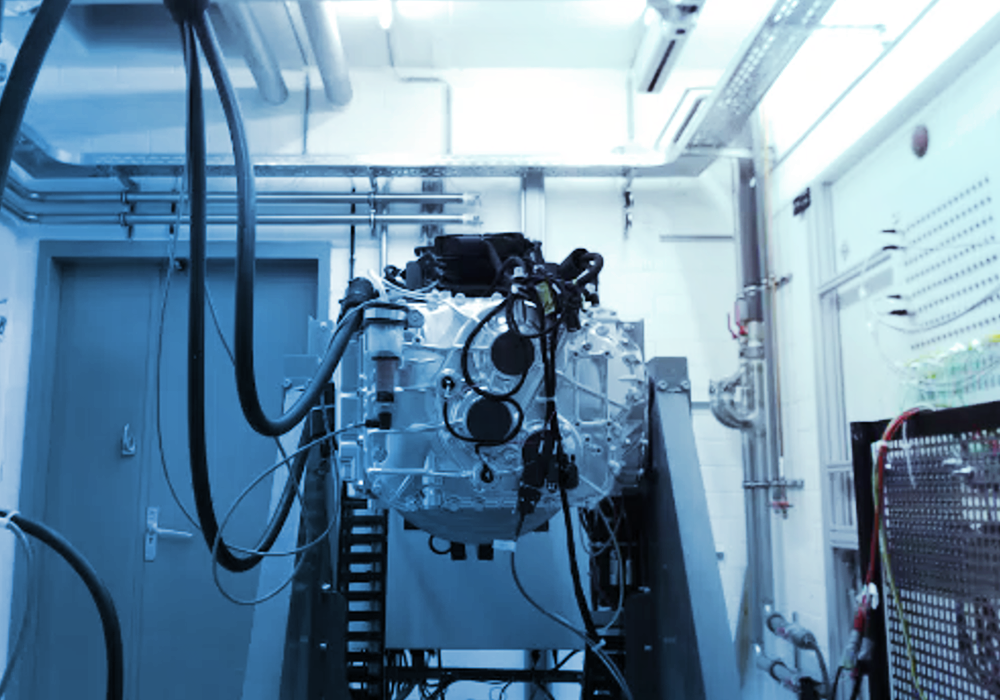
Experienced in testing of all types of modern drive systems, we analyse and optimise each individual component in great detail: hydraulic components, gears, electric drive components, clutches, transmissions syncs, engine / gearbox bearings and decoupling elements. I.e., to validate calculated gear design, the manufactured parts are geometrically measured and tested to determine the contact pattern, the acoustic running behavior and the gear breakage. Electrical machines and power electronics are tested on dynamometers regarding electrical performance, mechanical design, and thermal design.

From components and systems to aggregate tests, are test centers and test experts allow complete testing of your solutions. At our engine test benches, we study the combustion engine´s primary data such as power, torque, consumption, its mechanical properties and its thermodynamics, considering the peripherals. For aggregate testing, i.e., analysis of critical operating parameters of oil systems provides insights into oil behavior and distribution in the unit with help of transparent housings, inspection windows and temperature and flow measurements.
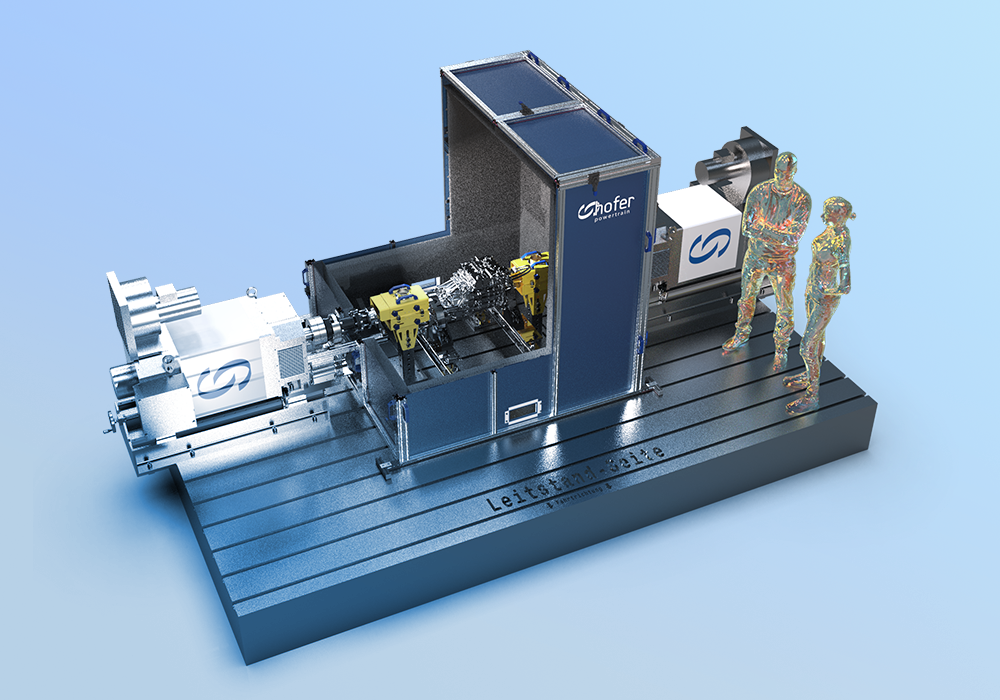
In our battery test field, a battery goes through the vehicle batteries’ complete life cycle with thermal load, charge and discharge cycles, thereby determining compatible battery and aging parameters. From technical analysis and benchmark tests to a complete examination of single cells to battery packs, various test approaches allow precise assessments to find ideal options for your battery solutions. Our concept validation tools use external parameters and simulate real-life behavior within the powertrain.
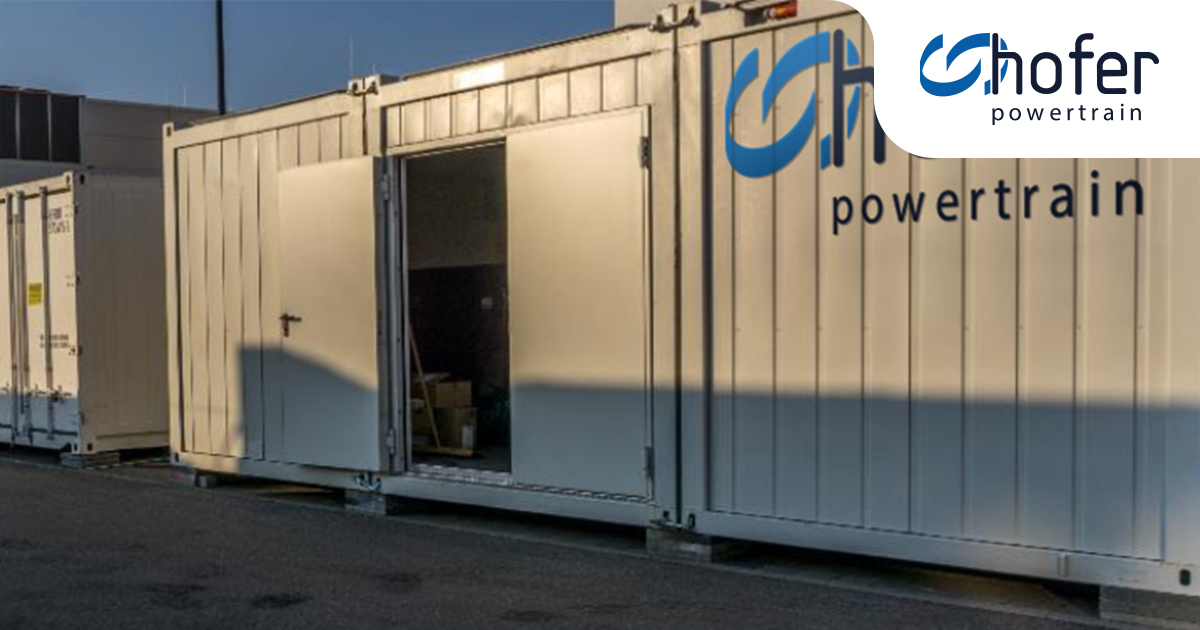
Our engineers´ expertise reach from motorcycles, tractors, and trucks to cars and supercars. In vehicle testing allows further calibrations for more comfort, reducing unwanted noises and overall efficiency of the powertrain. The experiences we gained through a large number of different projects enable benchmarking and correct evaluation by comparing measure data from various projects and development phases, from the demonstrator vehicle to the end-of-line data at the end of production and can be performed on the road or on the chassis dynamometer.
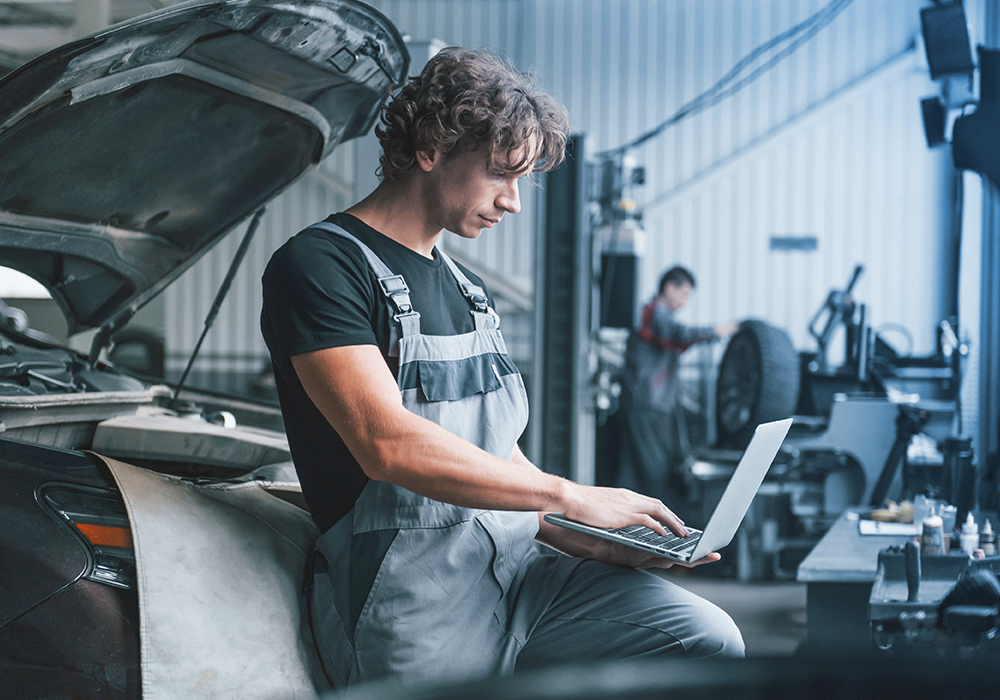
A variety of specialised test blocks for your special testing field can be provided. We build and deliver test rigs for testing pedal systems, from hydraulic components to end-of-line testing at the end of the production line. Additionally, our offer includes the mechanical structure, the control of the test bench and the required documents, e.g., CE marking.